A Look behind Congleton Certified #001
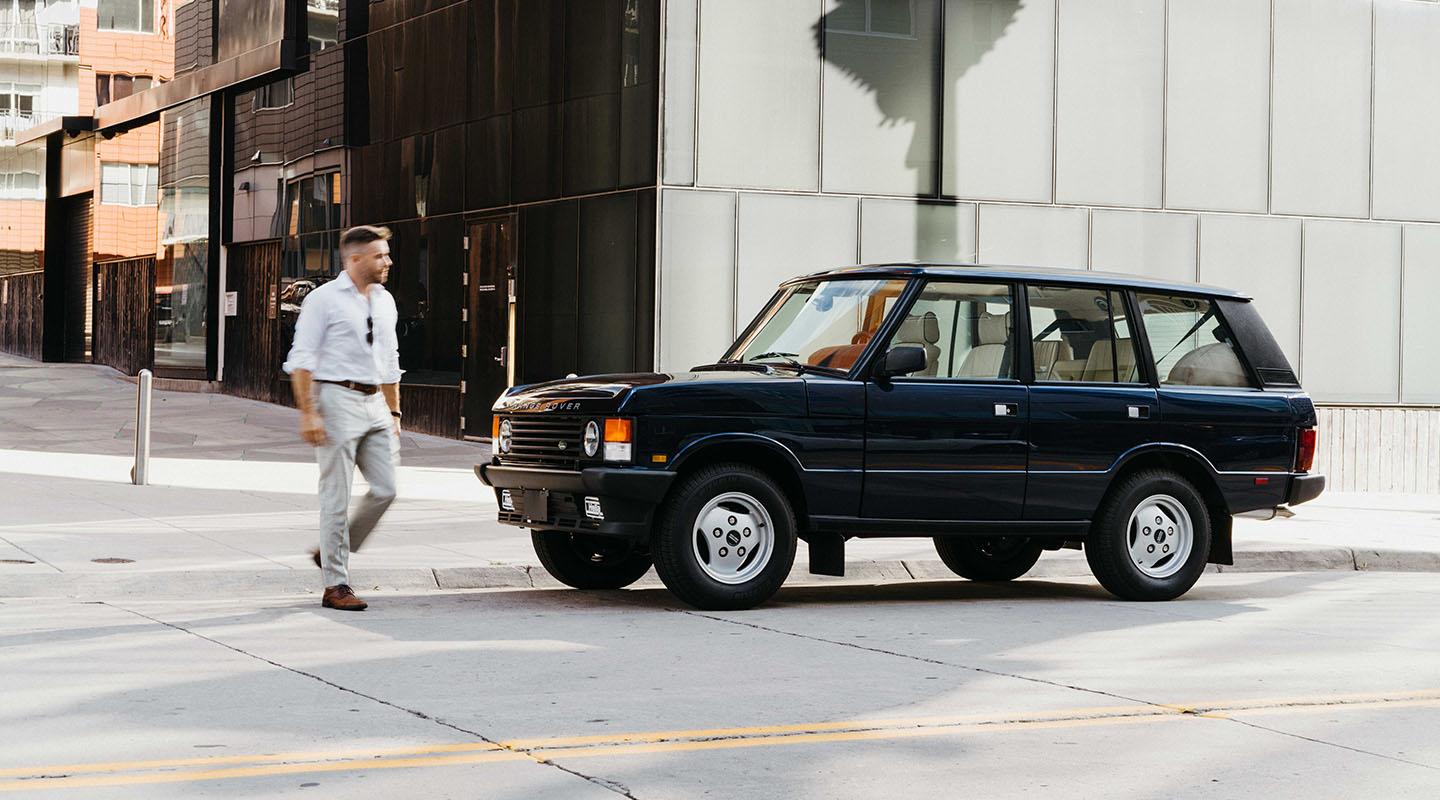
Certified #001, the Denver Project, was our first attempt at a completely certified Land Rover restoration. I sourced a body that was corrosion-free out of the New Mexico desert. The customer’s vision was to have a classic body style but with performance hidden beneath. So we built the 5.0L engine for ultimate performance. Our client wanted a leather-wrapped dashboard, which was challenging and obviously not done on the regular. The color for the exterior was also a challenge as it was a new model range rover color, Loire Blue, that we had never worked with before. We took on both challenges and succeeded. And the truck is better for them.
The biggest challenge for this vehicle was building it the way I envisioned it in my head. I probably ended up putting every piece on and off the car at least three times until I got all systems and finishes to where I was happy with them. There are always ways to improve them that you can only see upon completion.
- Taylor Congleton, founder and owner of Congleton Service
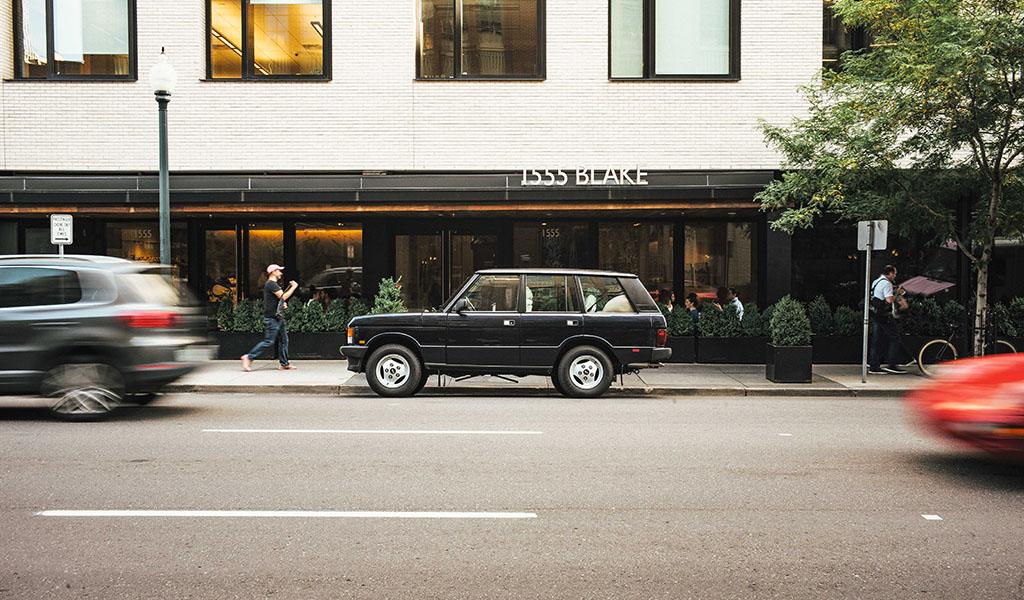
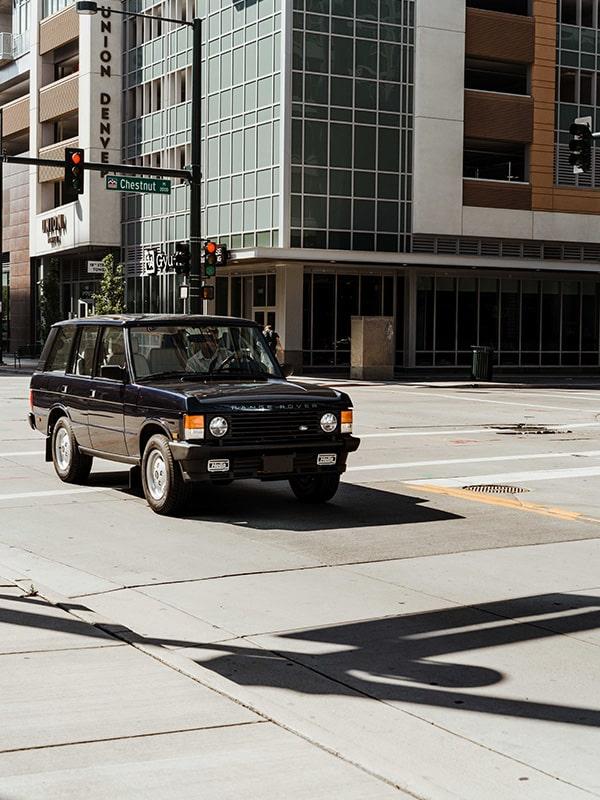
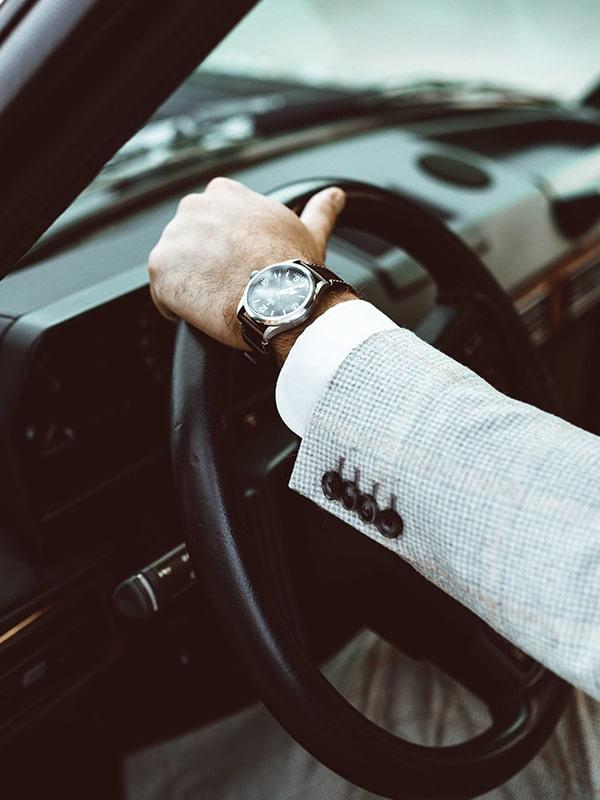
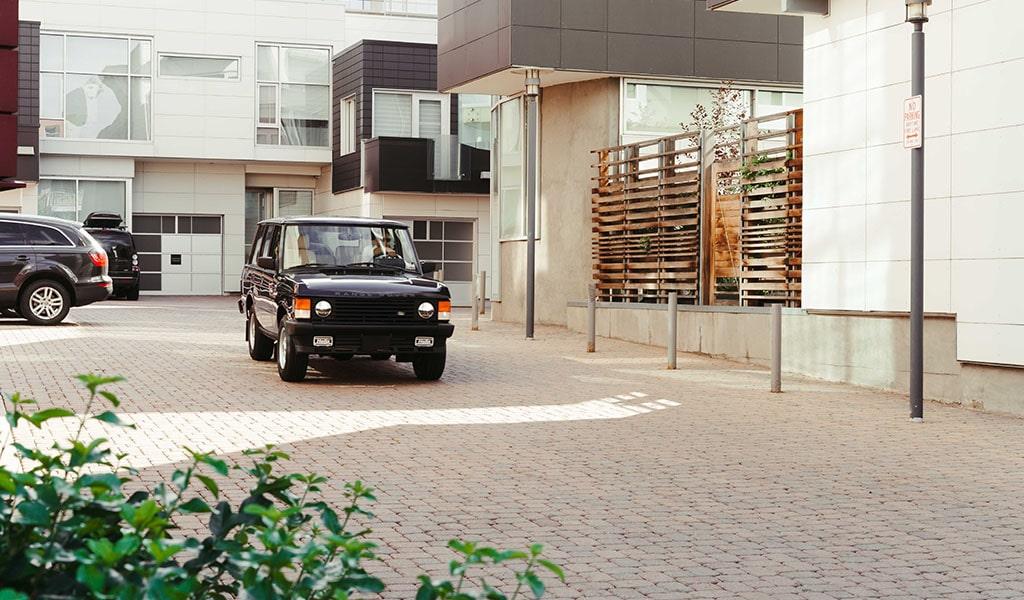
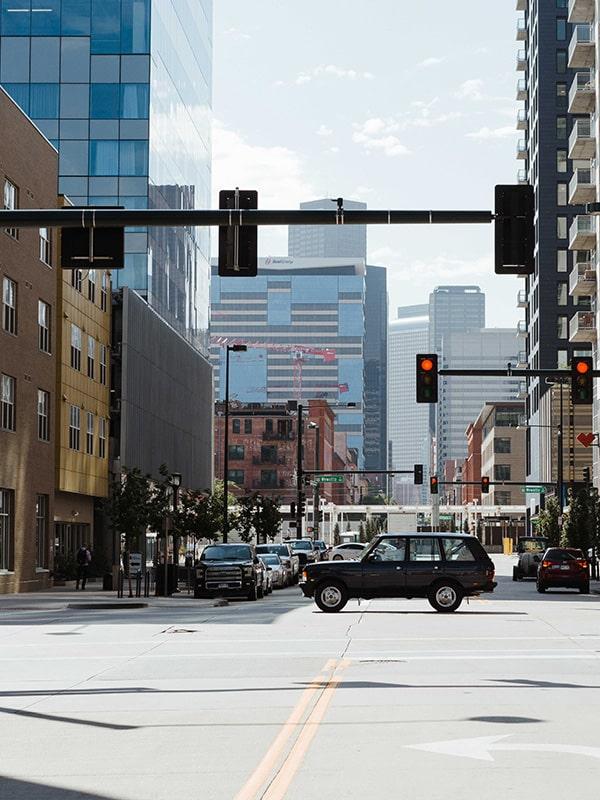
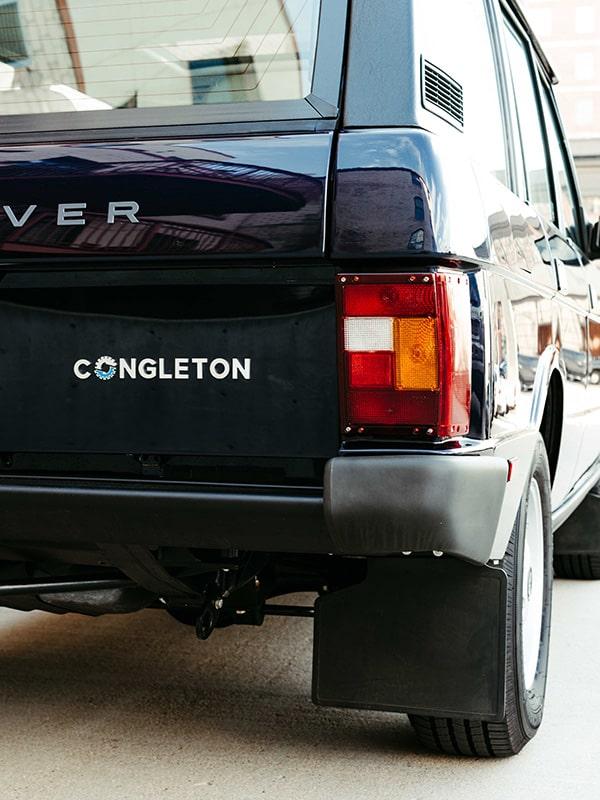